The heavy duty belt you need to move mountains
With five times the strength of conventional belts, the special Crows Foot Weave (CFW) fabric gives unmatched resistance to ripping and tearing. Whilst these belts are often a Custom Made line, they have become a stock item in two ranges. – Apex RipMaster-M PN1000/3. – Apex RipMaster-XCG PN1250/4. Apex RipMaster-M provides economic resistance and tearing with tough M Grade covers. Apex RipMaster-XCG gives extra protection with higher tensile strength. Our unique eXtra Cut & Gouge (XCG) covers provide a standout performance in applications with increased resistance to heavy impacts, abrasion and gouging required.
Fenner Dunlop utilises the concept of CFW to achieve higher levels of internal rubber penetration and increased rip resistance. Rip resistance is achieved by using lighter warp threads to accommodate heavier, weft threads. This culminates in a weave design that, if penetrated, will force the tear in a weft direction as opposed to straight along the belt.
With 50% more threads (ends) in the warp, 40% heavier weft yarn, 20% more weft threads (picks) and over twice the strength in the weft, this product is an excellent performer. Such a performance is often claimed to be matched, but, in service, the reality is alternatives that never achieve the same results.
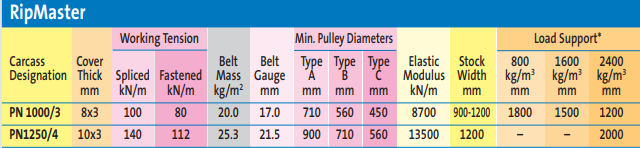
Pulley classifications
Type A – High tension, head, drive and tripper
Type B – Low tension, tail, bend and take-up
Type C – Low tension snub
Pulley diameters
Pulley diameters shown apply to belts operating at over 60% of maximum allowable working tension. Diameters of all pulleys must be reduced by 20% where belts are operating at less than 60% of allowable working tension. For belts at less than 30% of allowable tension, the diameters of Type A pulleys can be further reduced by 20%.
Working Tensions
Working tensions assume a reasonably well-maintained plant, with infrequent controlled starts and moderate impact.
For more severe service, ie: poor loading, frequently loaded or DOL starts, short time cycles then reduce the above values by 15%.
For extreme service, ie: poorly maintained plant, chemical aggression, bad loading and starting, then reduce the above values by 30%.