STORE McLIME BELT
History
Back in 1999 when Applied Conveyor first set up to supply quality Fenner Dunlop belting we were fortunate enough that engineers and maintenance staff saw the merit in using a quality product. However it was difficult to justify a 20-30% increase in investment based solely on a “salesman’s pitch”. Pricing was only part of the picture. The aim was to reduce belt maintenance costs, plan maintenance and reduce downtime to increase plant availability and reliability.
Situation
The fertiliser industry, particularly manufacturing and granulation, is extremely hard on equipment. The product is very hot, sticky, abrasive and dusty. All of these conditions could occur in one days production. Applied Conveyor completed a conveyor audit, logging belt lengths, widths, ply ratings, idler styles, drum diameters, drum laggings, splice details, belt speeds and tonnes per hr. All belt changes were recorded and monitored to gauge expected life. Some belts were changed from 3ply 4×1.5 to 3ply 5×1.5 and 4ply 6×2. Whilst the design checks confirmed 3ply was strong enough, but 4ply gave extra rubber cover thickness which extended the belt’s life. The Store incline belt carries the product produced from both Dens up into the No1 Superstore. This belt suffered with bottom cover wear due mainly to build up of fertilizer on the trough rollers. We installed an Fenner Dunlop Quarrymaster-M belt, 3ply initially then 4ply as volume and plant availability increased. The longest life recorded was 16 months from the Fenner Dunlop belt, the worst was 9 months from the Taiwanese belt. It was established that belt quality extend the operating life reducing downtime and resulted in considerable savings. Ravensdown also capitalized on thier maintenance plan to continually improve manufacturing conditions, uniformity of product, improved transfer points and reduced spillage. During this time to check progress a Fenner Dunlop 3ply 5×2 SAR grade belt was tried which lasted 16 months, then a Skellerup Quarrier belt was tried which lasted 10 months. At this point the cost effectiveness of Fenner Dunlop Quarrymaster-M became obvious. We had proved the FERTMASTER PN 500/3 4X2 SPECIAL COVERS on the No2 Den although this incline belt was the first conveyor to be fitted with FERTMASTER so we were confident it would show the same cost savings. Costs saving based on a 30 months.
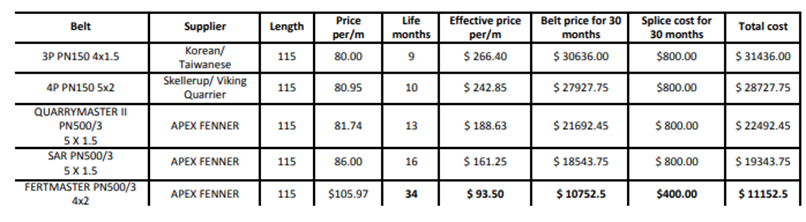